Enhancing 3D Printing Business with PLM Systems
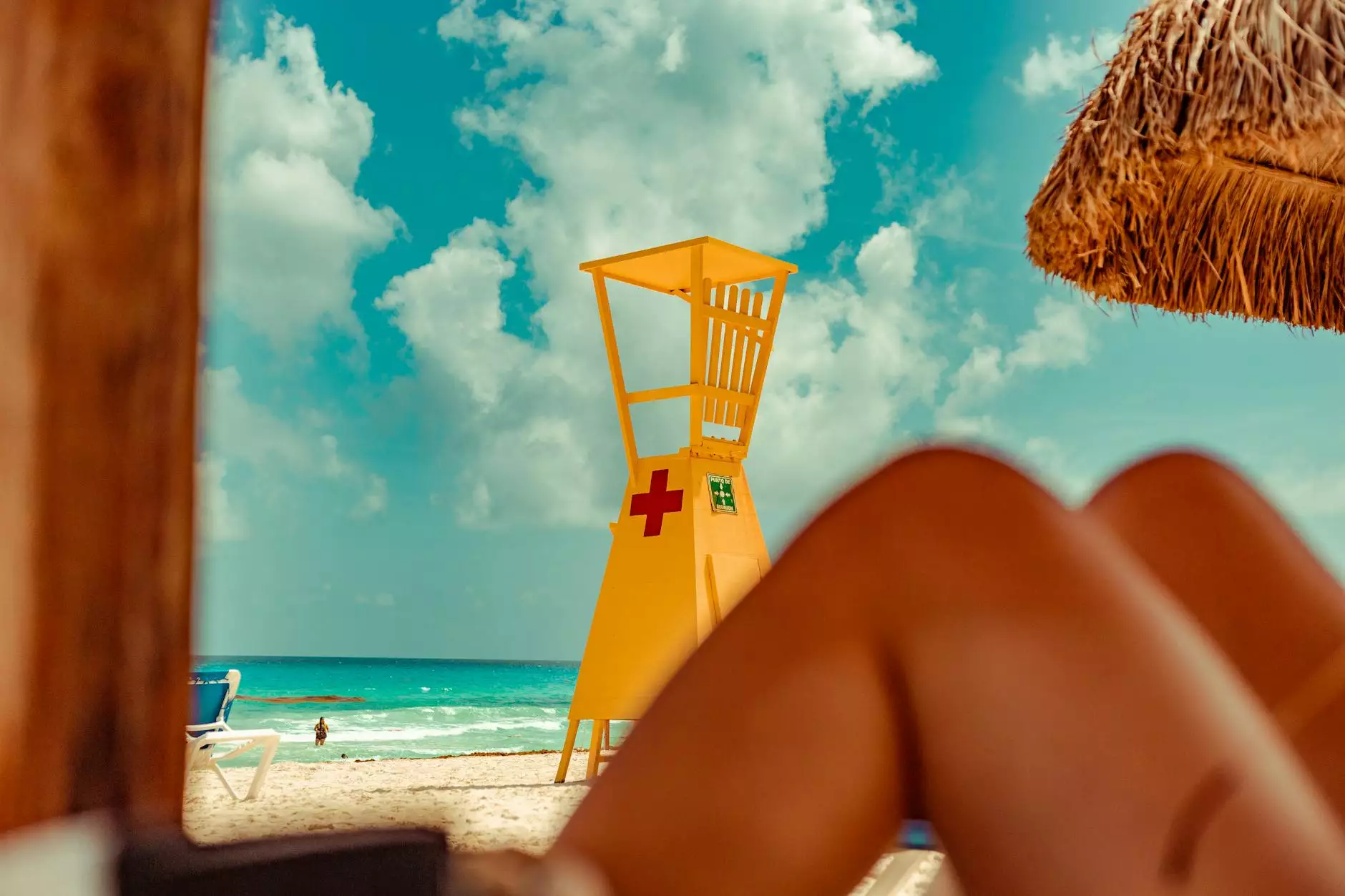
Product Lifecycle Management (PLM) is an essential strategy for organizations that aim to streamline their processes, especially in the rapidly evolving field of 3D printing. The evolution of manufacturing and product design mandates a need for improved methodologies to manage the lifecycle of a product effectively. This article will explore the profound impact of using a PLM system in the 3D printing industry, detailing its benefits and implementation strategies.
What is a PLM System?
A PLM system is a centralized solution that manages all aspects of a product’s lifecycle from inception, through engineering design and manufacturing, to service and disposal. It integrates people, processes, data, and technology, enabling organizations to make informed decisions throughout the product development journey.
Core Components of PLM Systems
- Product Data Management (PDM): Centralizing product data ensures that everyone in the organization has access to the most up-to-date information.
- Collaboration Tools: Enhancing communication among teams working on various aspects of product development.
- Document Management: Organizing and controlling documents related to the product lifecycle.
- Compliance and Quality Management: Ensuring that products meet legal and quality standards.
- Analytics and Reporting: Offering insights for better decision-making and continuous improvement.
The Importance of PLM in 3D Printing
As the demand for rapid prototyping and custom manufacturing grows, so does the complexity of product management. The integration of a PLM system within 3D printing practices brings numerous advantages:
1. Streamlined Development Processes
Introducing a PLM system streamlines development processes by providing a structured approach to managing product data. It allows for quicker iteration and adaptation, essential for 3D printing where design modifications may occur frequently.
2. Enhanced Collaboration
In a sector where teams may work on different geographical locations or time zones, a PLM system fosters collaboration. It enables real-time sharing of ideas, documents, and product specifications to ensure everyone is aligned with the project goals.
3. Improved Product Quality
Utilizing a PLM system assists in maintaining high standards of product quality. By implementing thorough testing and validation during the lifecycle, companies can identify defects early, reducing the cost and time associated with late-stage corrections.
4. Better Compliance Management
Regulatory compliance is vital, especially in sectors like aerospace and medical devices. A robust PLM system helps organizations manage and document compliance efforts efficiently, reducing risks associated with non-compliance.
5. Cost Efficiency
By minimizing errors and optimizing workflows, companies can save on costs that would typically arise from reworks and delays. A PLM system empowers businesses to manage resources effectively, leading to significant operational savings.
Key Challenges in Implementing a PLM System
While the benefits are substantial, companies may encounter several challenges during the implementation of a PLM system. These include:
- Change Management: Resistance to change is a common barrier, and organizations must engage stakeholders early in the process to ensure buy-in.
- Integration with Existing Systems: Organizations often rely on multiple software solutions. Selecting a PLM system that integrates well with existing tools is crucial.
- Data Migration: Transitioning existing product data into the new system can be a complicated task. Careful planning is necessary to maintain data integrity.
- Training and Support: Employees must be trained on the new system. Providing adequate support during and after implementation can ease the transition.
Steps to Effectively Implement a PLM System
To overcome these challenges and successfully implement a PLM system, organizations should follow a structured approach:
1. Define Objectives
Establish clear goals for what the PLM system should achieve. Consider aspects such as reduced time to market, improved collaboration, and enhanced compliance.
2. Engage Stakeholders
Involve all relevant stakeholders, including engineering, manufacturing, and marketing teams, early in the process to gather input and ensure alignment on objectives.
3. Choose the Right PLM Solution
Research various PLM software offerings to find one that best fits the organization’s specific needs, scalability, and compatibility with existing systems.
4. Data Migration Planning
Develop a comprehensive strategy for migrating existing data to the new system, ensuring accuracy and completeness throughout the transition.
5. Training and Change Management
Provide thorough training to users and establish a change management plan to help staff adapt to the new processes and tools.
6. Monitor and Optimize
Once implemented, continually monitor the system's performance and gather feedback from users. Regular reviews can help identify areas for further optimization.
Future Trends in PLM for 3D Printing
The integration of PLM systems with emerging technologies is set to redefine the landscape of 3D printing:
1. AI and Machine Learning
Leveraging artificial intelligence (AI) and machine learning within PLM systems can enable predictive analytics, enhancing performance and decision-making processes.
2. Internet of Things (IoT)
The IoT will allow better monitoring of products throughout their lifecycle, providing data that can be analyzed to improve future designs and production methods.
3. Enhanced Visualization Tools
Augmented reality (AR) and virtual reality (VR) can transform how teams visualize product designs, leading to more informed feedback and rapid iterations.
4. Sustainability Features
As businesses aim for more sustainable practices, PLM systems will increasingly focus on materials sourcing, waste reduction, and the overall environmental impact of products.
Conclusion
In conclusion, the adoption of a PLM system in the 3D printing industry represents a tremendous opportunity for businesses to innovate, collaborate, and thrive in a competitive market. By effectively managing every phase of a product's lifecycle, organizations can enhance their operational efficiency, improve product quality, and drive sustainable practices. As technology evolves, integrating PLM systems with advanced tools and methodologies will shape the future of 3D printing, allowing businesses to stay ahead of the curve.