Die Casting Manufacturer: Leading the Future of Metal Fabrication
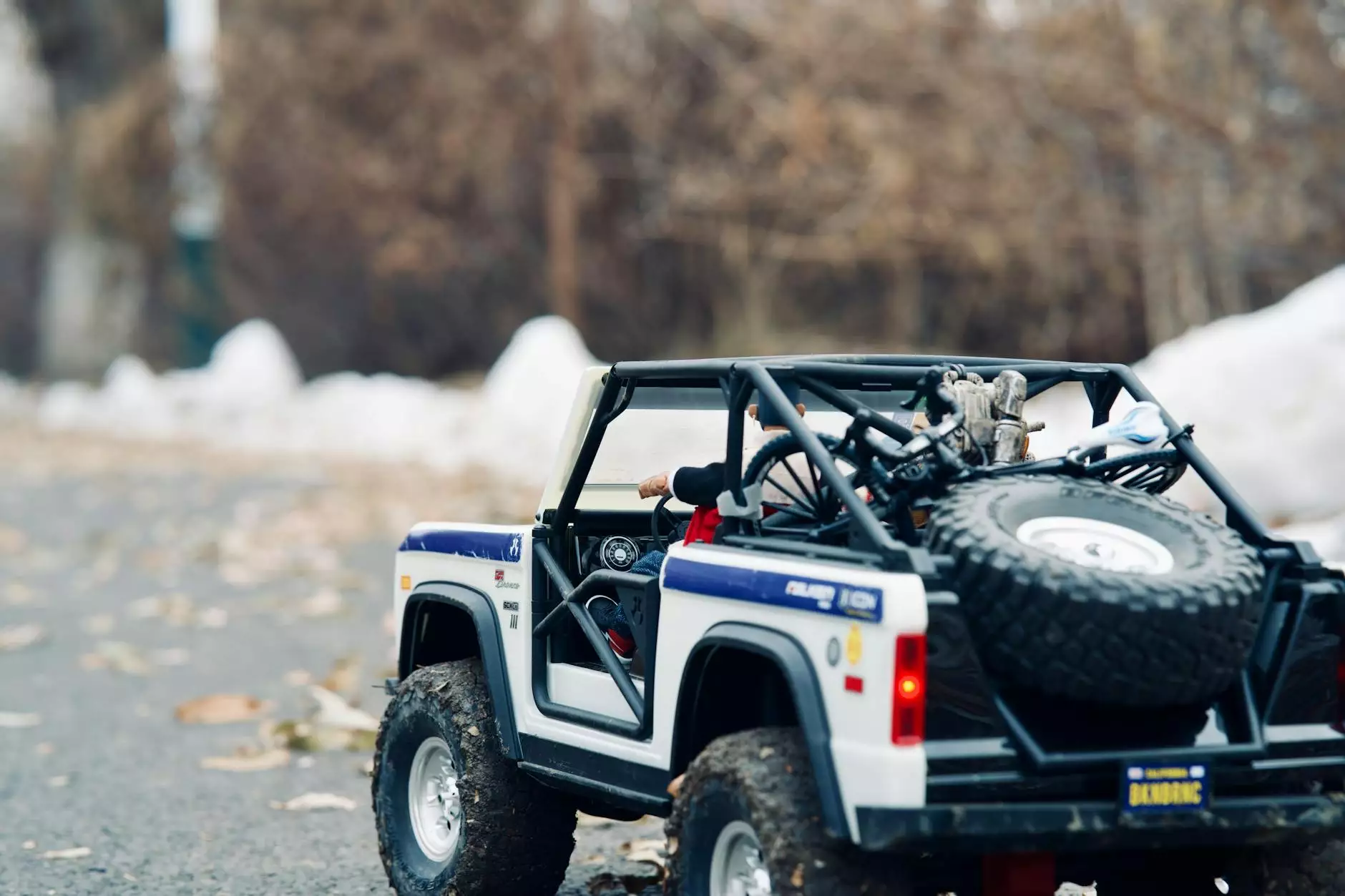
The world of manufacturing is a constantly evolving landscape, and at the heart of this evolution lies a critical technique known as die casting. As a prominent die casting manufacturer, DeepMould stands out by providing exceptional metal fabrication services that meet the demands of various industries. In this comprehensive guide, we will delve deep into the intricacies of die casting, its benefits, processes, applications, and the forward-looking innovations that make it a cornerstone of modern manufacturing.
Understanding Die Casting
Die casting is a manufacturing process that involves injecting molten metal into a mold to create complex shapes with high precision. This method is renowned for its ability to produce lightweight and durable components, making it a preferred choice for industries ranging from automotive to consumer electronics.
How Die Casting Works
The die casting process consists of several key steps:
- Preparation of the Die: The die, which is typically made of steel or iron, is carefully designed and prepared. It consists of two halves that create the mold for the desired part.
- Melting the Metal: The selected metal, often aluminum, zinc, or magnesium, is heated until it becomes molten.
- Injection: The molten metal is injected into the die at high pressure, filling all cavities of the mold.
- Cooling: After the metal has filled the die, it is allowed to cool and solidify.
- Demolding: Once cooled, the die is opened, and the completed part is ejected.
- Finishing: The final step involves any necessary finishing processes, such as machining, coating, or assembly.
Types of Die Casting
There are two primary types of die casting processes that manufacturers utilize:
- Permanent Mold Casting: This method involves using a reusable mold made of metal. It allows for high precision and durability.
- Die Casting with Sand Molds: This technique uses sand molds and is typically employed for lower quantities of production.
Advantages of Die Casting
The use of die casting comes with numerous benefits that make it an attractive option for manufacturers:
- High Precision: Die casting produces parts with excellent dimensional accuracy, reducing the need for extensive post-processing.
- Complex Shapes: It allows for the creation of intricate designs and geometries that may be impossible with other methods.
- Consistent Quality: Once a die is created, it ensures uniform quality across all parts produced.
- Efficiency: The quick cycle times associated with die casting increase production speeds significantly.
- Material Savings: Minimal waste due to the ability to recycle scrap metal enhances sustainability.
Applications of Die Casting
Die casting has a broad range of applications across various industries. Below are some key sectors that benefit greatly from this manufacturing process:
- Automotive: Die casting is widely used for producing components like engine blocks, transmission housings, and various interior and exterior parts.
- Electronics: The production of casings for mobile phones, computers, and other electronic devices often involves die casting for its precision and lightweight properties.
- Aerospace: Components for aircraft, including housings and brackets, benefit from the strength-to-weight ratio achieved through die casting.
- Consumer Goods: Household items like kitchen appliances and furniture components frequently utilize die casting to ensure aesthetic appeal and durability.
Choosing the Right Die Casting Manufacturer
When selecting a die casting manufacturer, several factors should be considered:
Expertise and Experience
Look for manufacturers with a proven track record in the industry. Experienced manufacturers will have encountered various challenges and developed solutions that can benefit your project.
Technology and Equipment
Advanced technology in die casting machinery can significantly affect the quality and efficiency of production. Ensure that your manufacturer uses up-to-date equipment and techniques.
Quality Control
Ask about their quality assurance processes. Reliable manufacturers implement rigorous quality control measures to maintain high standards across production runs.
Customer Support
Choose a manufacturer known for excellent communication and support throughout the project. Strong partnerships often lead to better collaboration and results.
The Future of Die Casting Manufacturing
The die casting industry is advancing rapidly, adopting new technologies and practices to meet modern challenges. Here are some promising trends shaping the future:
Smart Manufacturing
The integration of the Internet of Things (IoT) is set to revolutionize die casting. Smart sensors can monitor production in real-time, identifying inefficiencies and minimizing downtime.
3D Printing of Die Cast Components
3D printing technology is making its way into die casting by allowing for rapid prototyping of molds. This can streamline the production process and reduce the lead time for new components.
Sustainability Practices
As industries strive for sustainability, die casting manufacturers are focusing on reducing energy consumption and utilizing environmentally friendly materials in their processes.
Conclusion
In conclusion, die casting is a pivotal process for modern metal fabrication, offering a wide array of benefits, including precision, efficiency, and adaptability. As a premier die casting manufacturer, DeepMould is dedicated to harnessing advancements in technology to provide exceptional products to various industries. As we look to the future, the evolution of die casting will undoubtedly continue to enhance manufacturing capabilities, driving innovation and enhancing competitiveness in the global market.